Technology and Materials
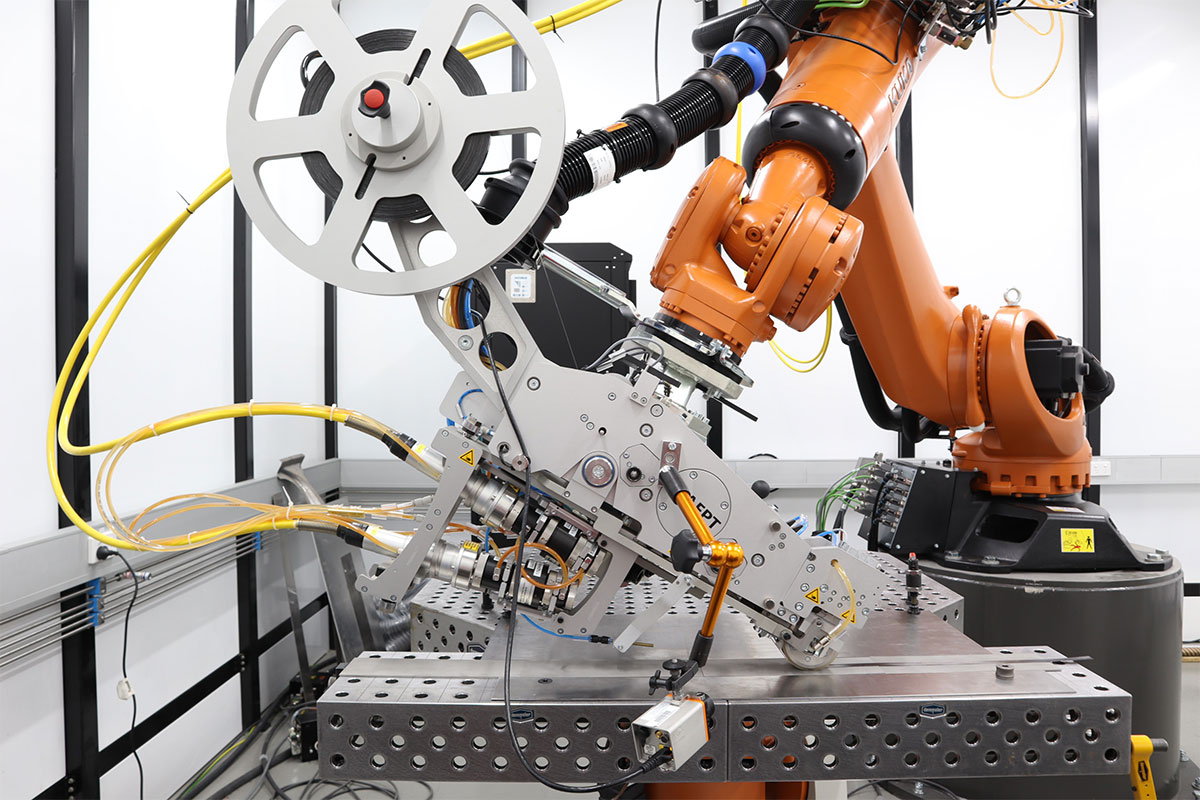
We are experts in Automated Fibre Placement (AFP), and work in partnership with leading equipment developers to deliver composites for a range of projects spanning the space, energy, construction, aviation and defence sectors meeting specified stiffness, strength, torsion, weight, or operating temperature requirements.
This method of manufacturing involves automated layering of carbon composite pre-preg tapes, bringing with it a range of benefits:
- Efficiency – the process is low waste and low energy.
- Precision – component integrity, stiffness and fibre orientation can be easily tailored.
- Speed – a comparably quick manufacturing process with no curing required.
- Scalability – manufacturing can be scaled up easily and quickly.
- Consistency – variation is minimal, even at large scale.
Learn more about the process and our equipment from our partners AFPT.
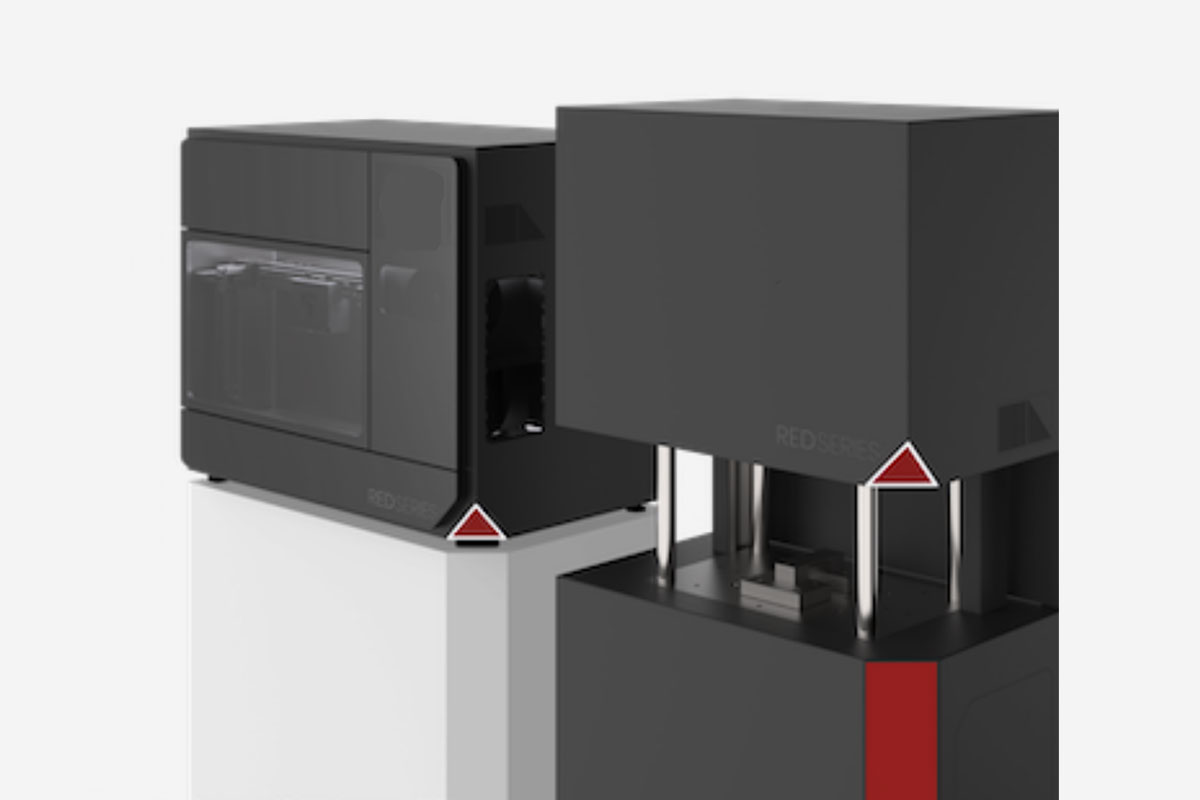
With the Additive Fusion Technology (AFT) it is possible to design and create continuous fibre components with complex geometry, free of the limitations of conventional CNC-driven machining techniques. It combines innovative additive manufacturing equipment and advanced post-processing technology working hand in hand to improve strength and density to give you the best quality output while reducing excess material waste.
Further benefits of AFT include:
- Efficiency – the process is low waste and low energy.
- Precision – component integrity, stiffness and fibre orientation can be easily tailored.
- Design – Geometrical design freedom.
- Speed – Fast design / prototype / production turnaround cycles.
- Performance – Increased material strength by elimination of inherent low-density feature of 3D printing.
- Cost – Cost competitive to metallic serial production.
Learn more about the process and our equipment from our partners 9T Labs.
We are the only company world-wide that can offer a combination of AFP and AFT which unlocks the design freedom for high-performance carbon composite parts with reduced part count. These two technologies are complementary and highly compatible. With our design and manufacture expertise, we can support you to reach your lightweight goals such as reducing fuel consumption or increasing the payload of your aerostructure.
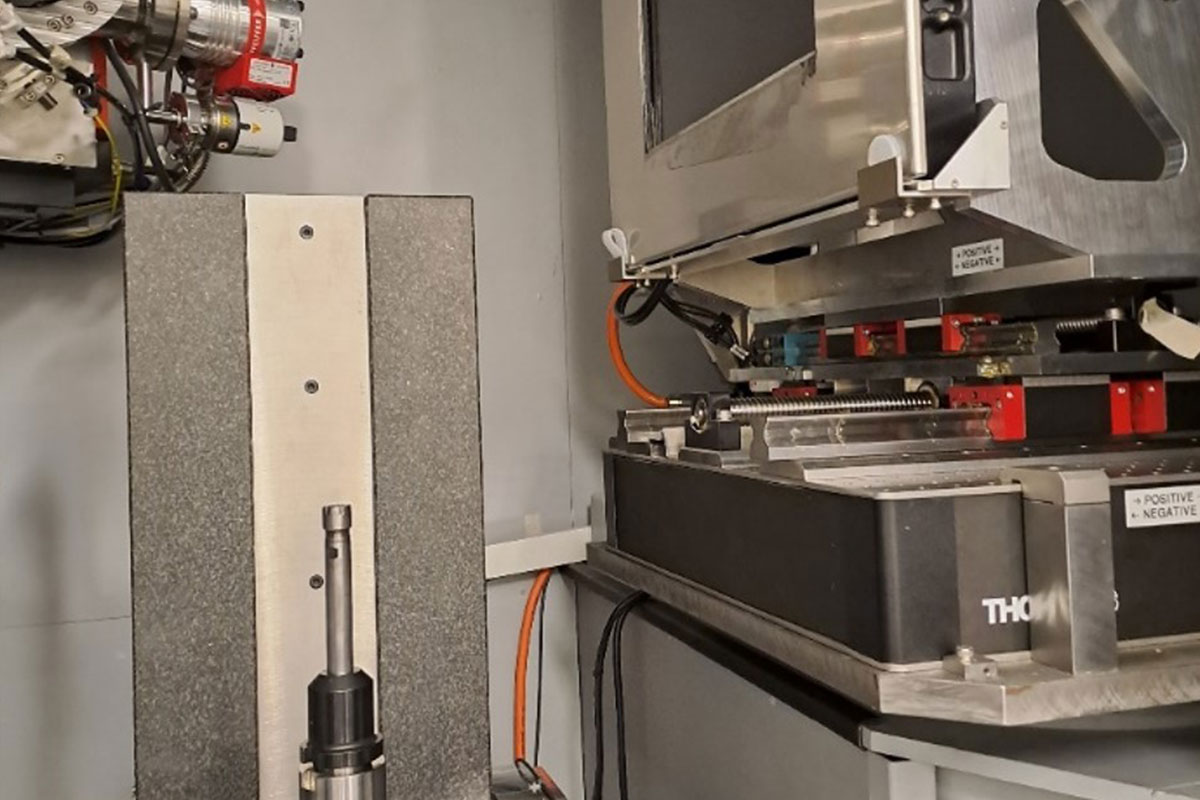
Our 3D analysis capability is utilising the Micro Computed Tomography laboratory hosted at the Australian National University (ANU CTLab) which is a world-leading facility in CT imaging, reconstruction and visualisation. All images we utilise for our advanced diagnostic work are acquired on HeliScan™ micro-CT instruments that utilise state-of-the-art X-ray helical scanning and innovative iterative reconstruction technologies.
For smaller samples, we use ANU micro-CT instruments to acquire high-resolution high-fidelity tomograms and subsequently probe and analyse their 3D microstructure at up-to sub-micron accuracy and resolution. Larger volume samples and high-density materials can be imaged on a universal CT scanner equipped with a high-flux high-energy reflection X-ray source (up to 300 kV) and capable of over 1000 mm vertical travel. Working with the high-quality images captured in the ANU CTLab we can provided the highest quality analysis, however our expertise can be applied to 3D images captured in other labs.
High resolution | Large volume | Whole core | |
X-ray source | 150 kV | 50 – 180 kV | 50 – 380 kV |
Voxel size | 1 µm | 2 µm | 10 µm |
Sample diameter | 1 – 100 mm | 3 – 200 mm | 25 – 300 mm |
Vertical travel | 100 – 200 mm | 500 mm | 1000 mm |
Our manufactured products can meet the most demanding requirements thanks to our high-performance carbon-fibre/thermoplastic (PA6, PES, PEEK) composite materials.
Our material achieves extremely low out-gassing in operation, which is a good candidate for compatibility with optical components in space and making it suitable for extreme radiation. These materials are endorsed by NASA and the aviation industry for use in these highly regulated industries.
Our processes are not limited to just carbon composites. We can also process other thermoplastic composites with, for example, glass-fibres.